PIR PP
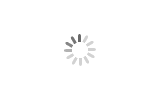
PIR PP (PostIndustrial Recycled Polypropylene) - Post-industrial recycled polypropylene
PIR PP is a kind of environmentally friendly plastic that is recycled after the waste polypropylene materials (such as scraps, waste materials, etc.) generated in the industrial production process are recycled. As a highly recyclable plastic, polypropylene (PP) has excellent mechanical properties, chemical resistance and high temperature resistance, and PIR PP is widely used in a number of industries, especially in areas requiring high strength and stability.
Product Details
1. Main sources of high-quality PIR PP recycled feedstock
Waste from the production process
During the production of polypropylene products, waste materials such as runners, trimmings and rejects are often generated. These wastes are unused and pure, and are an important source of high-quality industrially recycled polypropylene.
Recycling Source Example:
Runner material: the part of the runner produced during the injection molding process.
Edge: The edge waste generated in the process of product trimming.
Non-conforming products: inferior or defective products produced in production.
Waste from the plastics processing industry
In the plastics processing industry, the processing of polypropylene materials generates a number of wastes, such as extrusion wastes and trimming wastes. These wastes are recycled and processed to produce high quality recycled polypropylene.
Recycling Source Example:
Extrusion Waste: Waste from the extrusion process of polypropylene materials.
Trimming waste: Waste generated during the trimming process of polypropylene products.
recovery process
The recycling process for high quality industrially recycled polypropylene typically includes the following steps:
Collection and Sorting: Polypropylene wastes from industrial production processes are collected and sorted according to material and color.
Cleaning and pre-treatment: The recycled polypropylene waste is cleaned to remove surface dust and impurities.
Pulverizing and melting: Cleaned polypropylene waste is pulverized and subsequently processed into recycled pellets through a melting process.
Filtration and pelletizing: Filtering technology is used to remove tiny impurities from the molten polypropylene to ensure the purity of the recycled material, which is then pelletized.
Quality testing: quality testing of recycled pellets to ensure that their performance meets the relevant standards and application requirements.
2. Strict quality control
PIR PP undergoes stringent quality control during the manufacturing process to ensure that the recycled material meets strict industry standards. Each batch of PIR PP raw material undergoes a number of performance tests such as tensile strength, impact resistance, heat resistance, etc. to ensure its reliability and high performance in different applications.
3. Excellent performance
High Strength and Durability: PIR PP has high tensile strength and abrasion resistance, making it suitable for application scenarios that are subjected to high loads and prolonged use.
Chemical resistance: PIR PP has good resistance to most chemicals (such as acids, alkalis, salt solutions, etc.) and is suitable for use in chemical environments.
High temperature resistance: Polypropylene has good high temperature resistance, can withstand high working temperature, suitable for high temperature environment.
Good processability: PIR PP has good fluidity and processability, suitable for injection molding, extrusion and other processes to meet the needs of different shapes and sizes of products.
4. Environmental protection and sustainability
By recycling industrial wastes, PIR PP effectively reduces waste accumulation in the production process and meets the environmental requirements of sustainable development.The use of PIR PP materials not only helps reduce the need for new polypropylene raw materials, but also effectively reduces environmental pollution.
5. Cost-effectiveness
Since the raw material of PIR PP comes from recycled waste, its production cost is relatively low. This makes PIR PP a cost-effective plastic material suitable for use in mass production, helping companies to reduce production costs while meeting the market demand for environmentally friendly materials.
Application area
Automotive industry: Used in automotive interior parts, external plastic parts (such as bumpers, dashboards, etc.) to provide high strength and durability.
Home appliance industry: such as TV shell, refrigerator parts, washing machine plastic parts, etc., with good chemical resistance and stability.
Packaging industry: Used in the production of packaging materials, containers, bottle caps, etc., to ensure good durability and cost effectiveness.
Industrial applications: such as various industrial containers, drums, pallets, etc., with high wear resistance and impact resistance.
Product advantages
High strength and durability: suitable for long-term high load or high strength requirements of the product.
Chemical resistance: Good resistance to acid, alkali, salt and other chemicals, suitable for chemical packaging and storage.
Good high temperature resistance: can withstand high temperature environment, suitable for automobiles, home appliances and other industries that need high temperature resistance.
Environmental protection: Through recycling waste polypropylene, reduce the dependence on petroleum resources, help reduce the accumulation of waste plastics, in line with environmental protection requirements.
Economy: The use of recycled materials reduces production costs and provides enterprises with a more competitive price advantage.
Production and technology advantages
Advanced recycling technology: Through modern recycling technology and optimized processing technology, to ensure that the quality and performance of PIR PP materials meet industrial standards.
Adapt to a variety of processing methods: support injection molding, extrusion and other processing processes, to meet the needs of different shapes and sizes of products.